
Maximize Equipment Uptime. Minimize Costly Downtime.
At MechSim3D, we specialize in helping businesses optimize maintenance management, planning, and reliability through our experienced consultancy services. We serve the civil earthmoving, agriculture, exploration drilling, and transport industries, ensuring operations run smoothly and cost-effectively.
Our goal is to minimize downtime and maximize equipment uptime, keeping your business productive and efficient.
​
We focus on companies with little or no existing maintenance strategies, planning experience, or structured reliability processes—providing the expertise needed to build a strong foundation for long-term success.
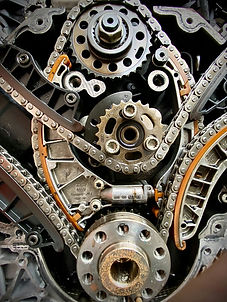
Management
Maintenance Management focuses on overseeing and optimizing maintenance activities to ensure equipment and assets operate efficiently. It includes scheduling, resource allocation, and performance monitoring to reduce costs and improve productivity.
Reliability
Reliability is about enhancing the dependability of equipment and systems by identifying risks, analyzing failure patterns, and implementing strategies like predictive maintenance to extend asset lifespan and improve operational stability.
Planning
Planning involves proactively organizing maintenance tasks, including routine servicing, repairs, and replacements. It ensures the right resources, tools, and personnel are available at the right time to prevent unexpected breakdowns and delays.
Structure
Structure refers to establishing a well-defined maintenance framework, including people, policies, procedures, and workflows. A structured approach ensures consistency, accountability, and efficiency in maintenance operations, particularly for businesses with little or no existing strategies.
MechSim3D - Transform Your Maintenance Operations
Effective maintenance isn't just about fixing equipment when it breaks — it requires a structured approach that balances management, planning, reliability, and structure. At MechSim3D, we work closely with our clients, customizing our approach to fit their unique needs, industry challenges, and operational goals.
While businesses can implement comprehensive preventive maintenance strategies, we can also provide simple, cost-effective solutions — such as Excel spreadsheets and basic tracking systems — Ensuring that maintenance improvements don’t require a significant capital investment to get started. By reducing costs, improving efficiency, and integrating the latest technologies, we help businesses develop strong maintenance foundations that drive long-term success.
Whether you're looking to implement preventive maintenance, build a structured maintenance strategy from scratch, or just discuss your options our expertise can help your operations run smoothly, safely, and cost-effectively.

Breaking down
Maintenance Management
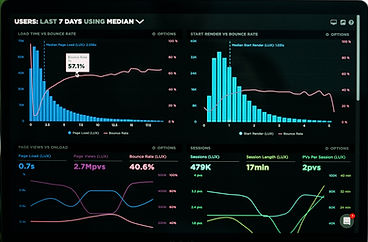
​Cost Reduction & Efficiency Gains – Effective maintenance management is about maximizing asset performance while minimizing costs. By optimizing maintenance workflows, reducing unnecessary downtime, and ensuring efficient use of resources, businesses can significantly lower operational expenses. This includes strategies such as:
​
-
Implementing preventive maintenance to reduce costly emergency repairs.
-
Streamlining work orders and scheduling to minimize wasted labor hours.
-
Utilizing spare parts management techniques to reduce inventory costs.
-
Analyzing downtime trends to identify and eliminate inefficiencies.
These cost-saving approaches increase overall equipment efficiency while allowing businesses to reinvest savings into further operational improvements​​​​
​​Technology & Digital Integration – Modern maintenance management goes beyond reactive repairs—it leverages technology to improve predictability, accuracy, and efficiency. We help businesses implement:
​
-
CMMS (Computerized Maintenance Management Systems) to automate maintenance scheduling, track work orders, and centralize asset data.
-
IoT Sensors & Real-Time Monitoring to detect potential equipment failures before they occur, reducing unplanned downtime.
-
Predictive Analytics to analyze equipment health and anticipate maintenance needs based on performance data.
-
Cloud-Based Reporting to provide real-time visibility into maintenance performance, key metrics, and overall asset reliability.
​​
Embracing digital tools, businesses can reduce downtime, improve decision-making, and create a more proactive maintenance environment, ultimately leading to higher productivity and lower costs.
Planning

​Preventive & Predictive Maintenance – A well-structured maintenance plan includes both short-term and long-term strategies to minimize failures and maximize equipment reliability.​​
​
-
Short-term preventive maintenance - Involves regular inspections, lubrication, and minor repairs to keep assets running smoothly and prevent immediate breakdowns. These tasks are typically scheduled based on time, usage, or manufacturer recommendations.
-
Long-term predictive maintenance - Uses advanced technologies such as condition monitoring and data analytics to anticipate failures before they happen. By analyzing historical trends and real-time equipment performance, businesses can extend asset lifespan, reduce unexpected failures, and optimize maintenance schedules.
Implementing a balanced preventive and predictive maintenance approach allows businesses to minimize downtime, reduce emergency repairs, and improve overall asset reliability.​​​​
​​​Flexible Engagement Models – Every business has different maintenance needs, budgets, and in-house expertise. We offer customized solutions to ensure companies receive the right level of support, whether they require basic guidance or a fully managed maintenance strategy.
​
-
Advisory Support – We provide consultations, audits, and recommendations for businesses looking to improve their existing maintenance strategies.
-
Hands-On Implementation – We help set up maintenance schedules, training programs, and cost-effective solutions, such as Excel-based tracking systems limited resources.
-
Ongoing Maintenance Management – For businesses looking for long-term support, we can provide fully managed maintenance services
​​
Offering flexible engagement options, we can ensure that businesses—regardless of size or industry—can implement a structured, effective maintenance strategy without unnecessary complexity or high costs.​​
​
Reliability

​Compliance & Safety Standards – Ensuring equipment operates safely, efficiently, and within industry regulations is critical to avoiding costly failures, legal penalties, and workplace hazards. We help businesses develop structured compliance processes by:
​
-
Identifying relevant safety and regulatory standards
-
Establishing proactive inspection routines to detect potential hazards before they become issues.
-
Creating documentation and reporting frameworks to ensure maintenance activities meet compliance requirements.
-
Training teams on best practices for equipment safety and legal obligations. B​y integrating compliance and safety measures into daily maintenance operations, businesses can reduce risks, enhance workplace safety, and improve overall equipment reliability.
​​
​​​​
Maintenance Metrics - To measure and improve equipment performance, we track key maintenance metrics:
-
MTTR (Mean Time to Repair) – Reducing repair times ensures that equipment is restored quickly, minimizing costly downtime.
-
MA% (Maintenance Availability Percentage) – Optimizing maintenance processes to maximize the time assets are available for use.
-
Compliance to Plan – Monitoring how effectively scheduled maintenance tasks are completed on time, ensuring reliability and operational efficiency.
​​​
​Tailored Solutions for Different Industries – Every industry has unique maintenance challenges, requiring customized strategies to maximize equipment dependability. Our approach adapts to the needs of sectors such as:
​
-
Agriculture – Maintaining farm machinery to prevent breakdowns during critical seasons.
-
Civil & Infrastructure – Ensuring construction equipment and infrastructure components are properly maintained to meet project timelines and regulatory standards.
-
Resources & Drilling – Implementing predictive maintenance strategies to reduce failures in high-demand, heavy-duty operations.
-
Transport & Logistics – Keeping fleets operational by monitoring vehicle uptime and scheduling preventive maintenance.​​
T​​ailoring maintenance strategies and tracking key performance metrics, can help businesses enhance equipment reliability, extend asset lifespan, and reduce costly disruptions.
Structure
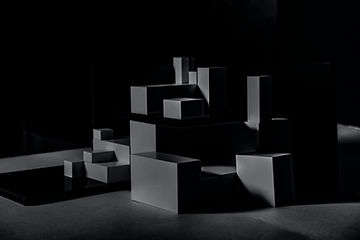
​Training & Knowledge Transfer – A well-structured maintenance system is only effective if the workforce understands and applies it correctly. We focus on educating teams at all levels, from frontline technicians to management, to build a knowledge-driven maintenance culture. This includes:
​
-
Workshops & Hands-On Training – Practical sessions to ensure staff can confidently execute maintenance tasks and troubleshooting procedures.
-
Technical Documentation & Guidelines – Creating user-friendly manuals, checklists, and best-practice guides to standardize maintenance workflows.
-
3D Simulation & Technology – Utilizing advanced 3D simulations to provide immersive, real-world training experiences, allowing teams to practice maintenance tasks in a risk-free, virtual environment before applying them in the field.
-
Knowledge Capture & Digital Databases – Ensuring critical maintenance knowledge is documented and stored in a digital database, allowing businesses to retain valuable expertise even when key personnel leave. This system provides a centralized knowledge base for training new employees and maintaining operational consistency.
-
Ongoing Support & Coaching – Helping teams adapt to new maintenance technologies, processes, and strategies with continued guidance.
​​
Empowering employees with the right knowledge, digital tools, and training methods, businesses can improve efficiency, reduce errors, and create a self-sufficient, future-proof maintenance workforce.
​​​​​​​​​​​​​​
​
​
Standardized Maintenance Processes – Inconsistent maintenance practices often lead to costly breakdowns, inefficiencies, and operational delays. We help businesses develop clear, repeatable maintenance workflows to ensure uniformity, efficiency, and accountability across all teams. This involves:
​
-
Defining Standard Operating Procedures (SOPs) – Establishing structured step-by-step maintenance instructions to ensure tasks are completed correctly and consistently.
-
Work Order Management Systems – Implementing digital or manual tracking systems to log maintenance activities, prioritize tasks, and assign responsibilities.
-
Preventive & Predictive Maintenance Schedules – Structuring routine servicing plans to reduce unplanned downtime and extend equipment lifespan.
-
Performance Audits & Continuous Improvement – Regularly reviewing maintenance data and team feedback to refine processes and eliminate inefficiencies.
-
Digital Integration for Process Standardization – Leveraging technology such as CMMS (Computerized Maintenance Management Systems) and IoT sensors to automate workflows, track maintenance history, and ensure data-driven decision-making.
​​
With structured and technology-driven maintenance approach, businesses can minimize risks, improve equipment reliability, and create a more accountable and efficient maintenance team that is resilient to workforce changes.
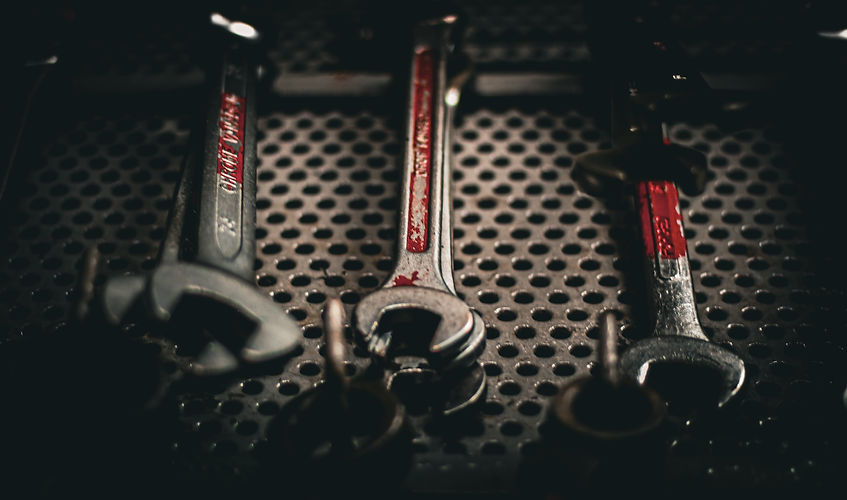
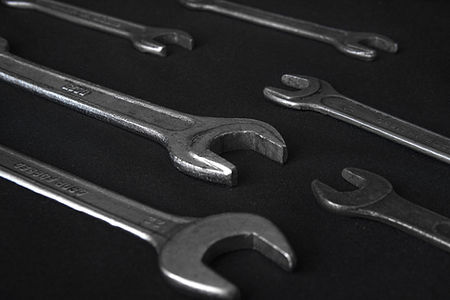